What Materials Are Natural Gas Pipes Made Of?
The durability and efficiency of natural gas pipes depend on the type of material used. The following main materials are commonly preferred:
Steel: Due to its high durability and pressure resistance, it is widely used in long-distance transportation lines between cities.
Polyethylene (PE): Known for its flexibility and corrosion resistance. It is generally preferred for city distribution lines.
Composite Materials: Combines the advantages of both steel and plastic materials. It can be used for medium-distance lines.
Natural gas pipe materials are the most fundamental factors determining the properties and lifespan of the pipes.
Factors Determining the Durability of Natural Gas Pipes
The durability of natural gas pipes depends on several factors. These factors can be summarized as follows:
Material Type: Steel pipes can withstand much higher pressure levels compared to polyethylene pipes.
Coating and Protection: Coating materials applied to the outer surface of the pipes prevent corrosion and ensure long life.
Usage Environment: Underground pipes are more protected against environmental factors compared to above-ground pipes.
Pressure Level: The maximum pressure value that pipes are exposed to is an important indicator of durability, especially in steel pipes.
Maintenance and Control: Regular maintenance and tests extend the life of the pipes and prevent potential problems.
Differences Between Underground and Above-Ground Natural Gas Pipes
Natural gas pipes can be used either underground or above-ground depending on the place of use. The differences between the two types are as follows:
Protection Level: Underground pipes are better protected from external effects since they are located under the ground. Above-ground pipes can be more affected by environmental conditions.
Access and Maintenance: Above-ground pipes are easier to access, while maintenance of underground pipes is more difficult and costly.
Aesthetics and Space Usage: Underground pipes are more advantageous aesthetically since they are not visible.
Corrosion Risk: Underground pipes have a higher risk of corrosion due to moist soil. Therefore, special coating is required.
Cost: Installing underground pipes requires more labor and cost compared to above-ground installation.
Methods for Preventing Corrosion in Natural Gas Pipes
Natural gas pipes are a crucial infrastructure component for safely transporting natural gas. However, these pipes can be exposed to corrosion due to environmental conditions. Corrosion shortens the lifespan of the pipes, leading to both economic losses and safety risks. Therefore, the following methods are commonly used to prevent corrosion in natural gas pipes:
Cathodic Protection
This method is used to prevent pipes from corroding through electrochemical reactions. It provides effective protection, especially for underground pipes.
Protective Coatings
Epoxy or polyethylene coatings applied to the pipes reduce the risk of corrosion. These coatings ensure that the pipes are resistant to environmental damages.
Regular Maintenance and Inspection
Regular checks of the pipeline allow early detection of corrosion signs and the taking of necessary measures.
Insulation Materials Used for Natural Gas Pipes
Insulation in natural gas pipes is critically important for both energy efficiency and preventing damages from environmental conditions. Here are the insulation materials commonly used in natural gas pipes:
Polyethylene Coatings
Polyethylene materials are both flexible and durable. These coatings protect pipes from both mechanical damage and corrosion.
Epoxy Coatings
Epoxy-based materials provide very effective protection, especially against the risk of corrosion in wet areas.
Glass Wool and Polyurethane
These materials provide thermal insulation, preventing energy loss during the transfer of natural gas.
Fiber Reinforced Plastic
Preferred in most pipelines due to its lightweight and long-lasting properties.
Similarities Between Natural Gas Pipes and Water Pipes
Both natural gas pipes and water pipes are durable, made from materials that transport liquids and gases. Both types of pipes are designed for long life, corrosion resistance, and safe transportation. They are typically made from steel, PVC, or galvanized materials.
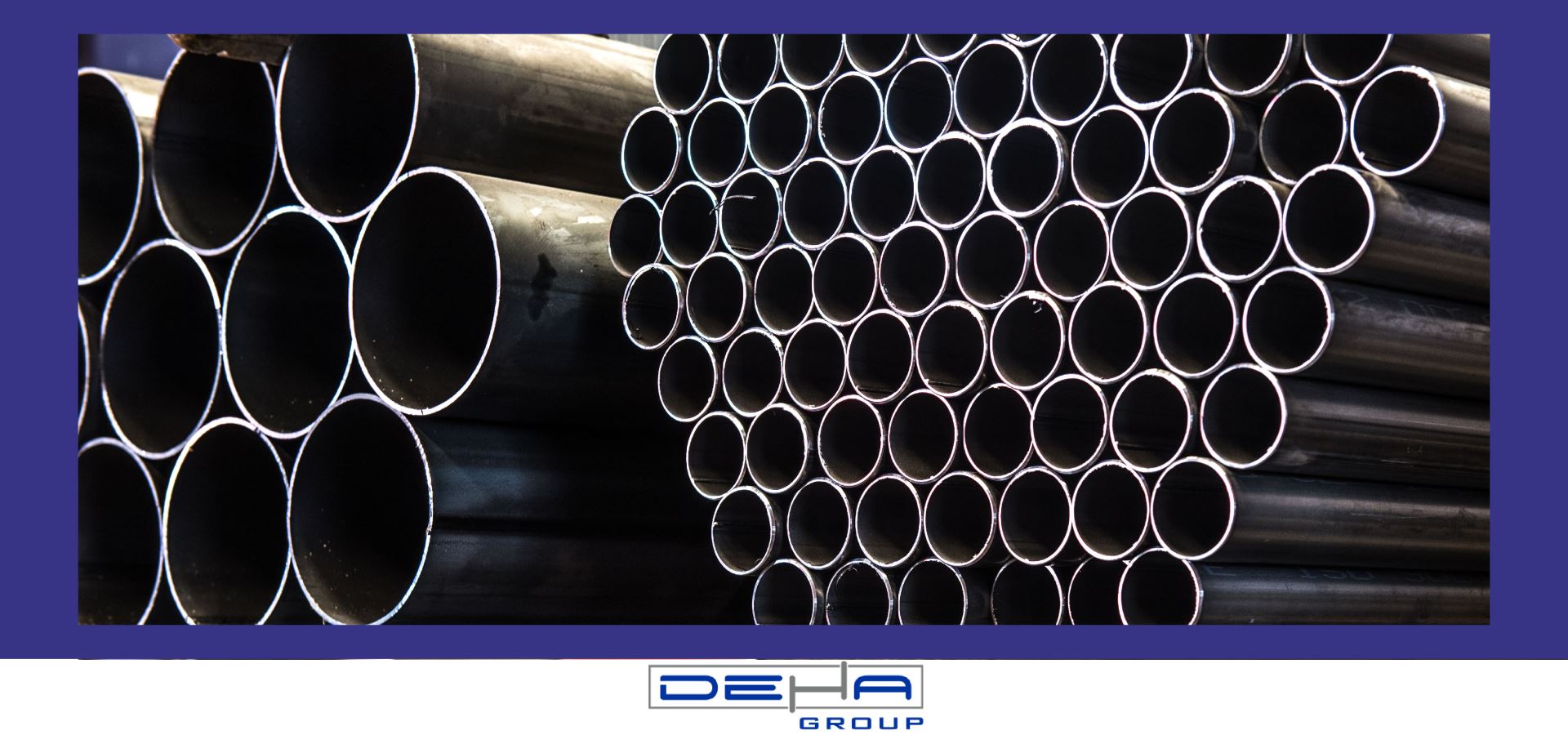
What Technological Developments Can Natural Gas Pipe Manufacturers Use?
Natural gas pipe manufacturers integrate modern technologies to enhance production quality and reduce costs. These technologies include:
Smart Material Technologies
Self-healing coatings can extend the life of the pipes. These materials can automatically repair micro damages.
3D Printing Technology
The production of pipe components with 3D printers can reduce production time and cost.
AI-Assisted Design
Computer simulations allow pipes to be designed more durably and efficiently.
NDT (Non-Destructive Testing) Technologies
These methods offer the opportunity for quality control of pipes without causing damage. Ultrasonic and radiographic tests fall under this category.
How Are Leak Tests Applied to Natural Gas Pipes?
Leak tests in natural gas pipes play a vital role in ensuring a safe flow of natural gas. The following steps form the basis of implementing these tests:
Pressure Tests
The pipeline is subjected to a specific pressure to check for any leaks.
Soap Water Test
Soap water is applied to pipe joints to watch for bubble formation. This is a simple but effective method to detect leaks.
Helium Leak Detection
For more sensitive tests, helium gas is introduced into the pipes to detect leaks.
Electronic Leak Detectors
Electronic devices detect gas leaks precisely.
Expected Innovations in Future Natural Gas Pipes
Natural gas pipe manufacturers aim to provide safer and more efficient solutions with technological advancements. Some of the innovations expected in future natural gas pipes include:
Nanotechnology
Nano coatings can make pipes more durable and lightweight.
Smart Sensors
Real-time monitoring systems can predict failures in advance by tracking pressure and temperature changes in the pipes.
Recyclable Materials
Eco-friendly materials can be frequently used in pipe production, reducing the carbon footprint.
Robotic Maintenance Systems
Robots that can travel inside pipes to detect and repair faults.
The features of natural gas pipes and the technologies used are of great importance in terms of both safety and efficiency. Natural gas pipe manufacturers benefit from a wide range of technologies, from corrosion prevention methods to insulation materials, to produce more durable and long-lasting pipes. Future innovations in this field are expected to contribute significantly to both the energy sector and the world at large.