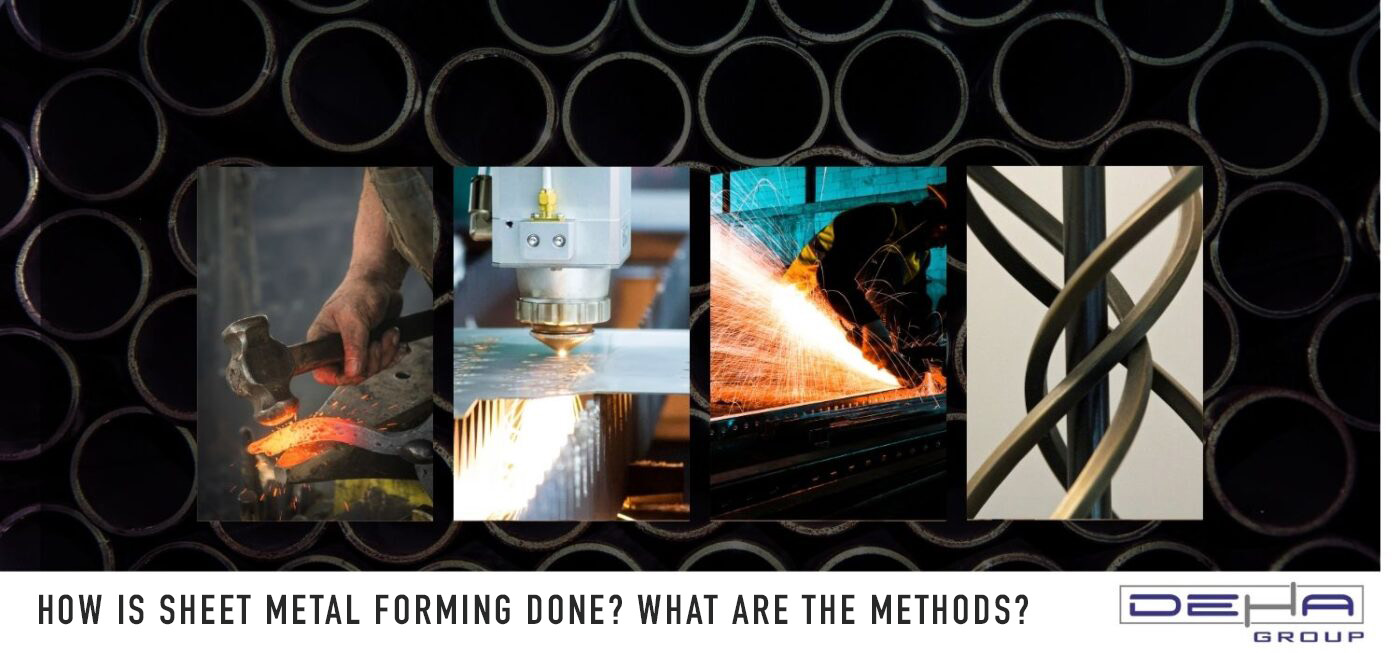
Sheet metal forming is a manufacturing process used to transform metal sheets into different shapes and sizes. This method, commonly used in the automotive, aviation, construction, and metal furniture industries, involves various techniques to process metal sheets and achieve the desired form.
Sheet metal forming is a manufacturing process used to transform metal sheets into different shapes and sizes. This process is widely used in the automotive, aerospace, construction, and metal furniture industries. Metal sheets are usually made from materials such as steel, aluminum, copper, and stainless steel, and are formed into the desired shape using various forming methods.
Cutting
The cutting process involves cutting metal sheets to the desired size and shape. It directly brings the sheets to the desired dimensions and forms the basis for other forming processes. Cutting is typically done using methods such as laser cutting, plasma cutting, or water jet cutting.
Laser Cutting: Laser light performs the cutting process by heating a specific point on the metal sheet. Laser cutting provides high precision and fast operation.
Plasma Cutting: Plasma cutting is a cutting method based on the principle of removing molten metal from the surface with a gas jet at high temperature. This method is usually used for cutting thick metal sheets.
Water Jet Cutting: Water jet cutting is a method where high-pressure water is sprayed onto the surface of the metal sheet to perform the cutting process. This method is used for cutting metal sheets of various thicknesses.
Bending
The bending process allows metal sheets to be bent at a specific angle. The sheet is typically bent to a certain angle with the help of a machine, such as a press brake or hydraulic press. The bending process is carried out considering the thickness, material, and bending angle of the metal sheet.
The bending process involves the following steps:
Die Selection: The angle at which the metal sheet will be bent is determined, and a suitable bending die is selected.
Placement of the Sheet: The metal sheet is placed correctly between the upper and lower parts of the bending machine.
Bending Process: The press brake or hydraulic press bends the metal sheet at a specific angle to form the desired shape.
Forming (Molding)
The forming process involves shaping metal sheets into the desired form with the help of molds. This process is usually done using hot or cold pressing methods.
Cold Pressing: Metal sheets are shaped at room temperature using a press. This method increases the durability of the metal sheets and allows for precise details.
Hot Pressing: Metal sheets are shaped at high temperatures using a press. This method makes processing the metal sheet easier during forming and allows for the production of more complex parts.
Punching
The punching process is used to make holes in metal sheets. Punching is usually done using a drill or punch press. The process is carried out considering the thickness, material, and location of the holes on the metal sheet.
The punching process involves the following steps:
Determining Hole Location: The locations for drilling holes on the metal sheet are determined.
Drill Selection: An appropriate drill is selected according to the characteristics of the holes.
Punching Process: Holes are drilled into the metal sheet using a drill or punch press.
Welding
The welding process is used to join metal sheets together. This process typically involves fusing the edges of the parts to be joined. The welding process may vary depending on the joining method and the welding material used.
The welding process involves the following steps:
Preparation of Parts to be Joined: The edges of the parts to be joined are cleaned and prepared.
Selection of Welding Material: A welding material appropriate for the material of the parts and the welding method to be used is selected.
Welding Process: The edges of the parts to be joined are melted and fused together, completing the welding process.
The sheet metal forming process is a manufacturing process that enables metal sheets to be transformed into different shapes and sizes. In this process, metal sheets are usually made from materials such as steel, aluminum, copper, and stainless steel and are shaped into the desired form using various forming methods.
Cutting
The cutting process involves cutting metal sheets into the desired size and shape. It directly brings the sheets to the desired dimensions and forms the basis for other forming processes.
Tools Used:
Laser Cutting Machine: Metal sheets are cut using laser light. Laser cutting provides high precision and fast processing.
Plasma Cutting Machine: This cutting method is based on the principle of removing molten metal from the surface with a gas jet at high temperatures. This method is generally used for cutting thick metal sheets.
Water Jet Cutting Machine: A cutting method where high-pressure water is sprayed onto the surface of the metal sheet to perform the cutting process. This method is used for cutting metal sheets of various thicknesses.
Bending
The bending process allows metal sheets to be bent at a specific angle. The sheet is usually bent to a certain angle with the help of a machine like a press brake or hydraulic press.
Tools Used:
Press Machine: The main tool used for bending metal sheets. The press brake or hydraulic press bends the metal sheet at a specific angle to create the desired shape.
Forming (Molding)
The forming process involves shaping metal sheets into the desired form with the help of molds. This process is usually carried out using hot or cold pressing methods.
Tools Used:
Cold Press Machine: Metal sheets are shaped at room temperature with the aid of a press. This method increases the durability of the metal sheets and allows for the attainment of precise details.
Hot Press Machine: Metal sheets are shaped at high temperatures with the aid of a press. This method allows for easier processing of the metal sheet during forming and enables the production of more complex parts.
Punching
The punching process is used to create holes in metal sheets. It is usually carried out using a drill or punching press.
Tools Used:
Drill: The basic tool used to make holes in metal sheets.
Punch Press: A special punching machine used in cases where a large number of holes need to be made.
Welding
The welding process is used to join metal sheets together. This process is usually performed by melting the edges of the parts to be joined together.
Tools Used:
Welding Machine: The main tool used for joining metal sheets.
Welding Wire and Gas: Welding materials used during the joining of metal sheets.
Sheet metal forming is an important manufacturing process that allows metal sheets to be shaped for use in various industries. This process includes various operations such as cutting, bending, forming, punching, and welding. Each operation requires precision equipment and expertise and determines the quality of the final product. Sheet metal forming methods include operations such as cutting, bending, forming, punching, and welding. These methods have a wide range of applications in industrial production and enable metal sheets to be formed in the desired shape and size. As a result, sheet metal forming is one of the cornerstones of modern industrial production and is a critical manufacturing process used in many sectors.