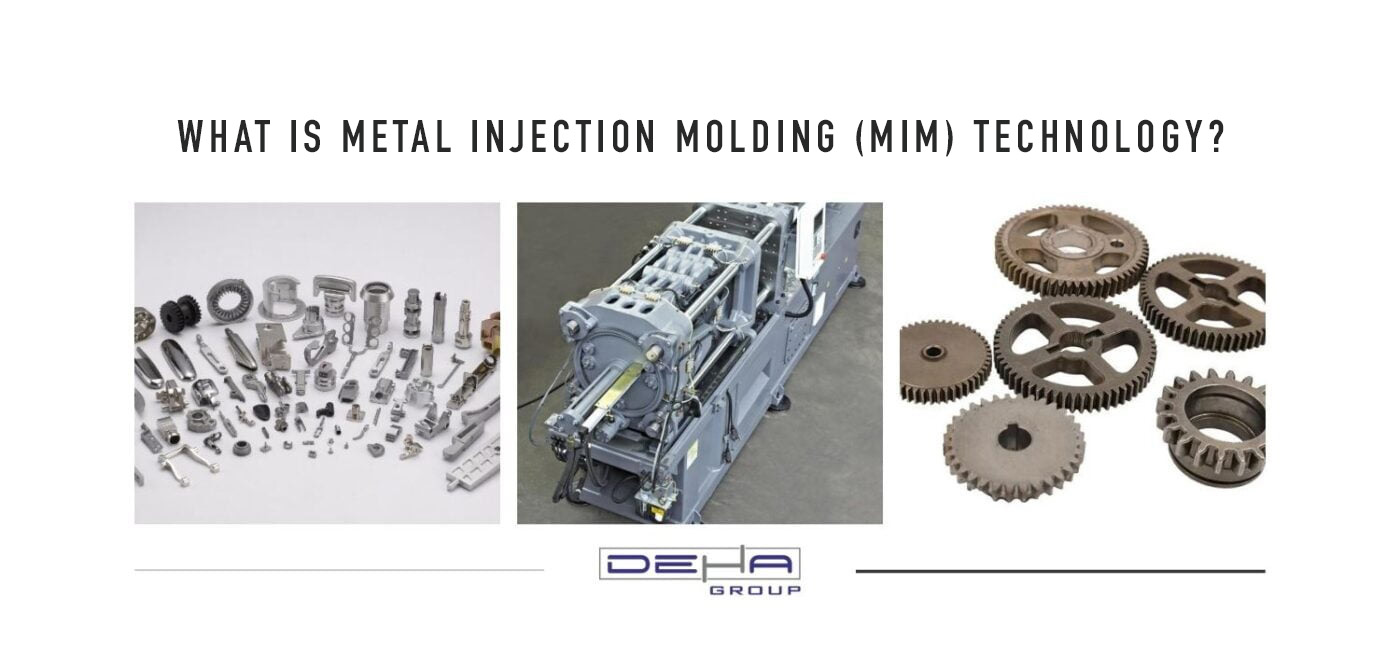
Metal Injection Molding (MIM) is the process of shaping a feedstock made by mixing metal powders and polymer binders through the injection molding method, followed by sintering to produce dense metal parts. This method enables the production of small metal parts with complex geometries, high precision, excellent surface quality, and superior mechanical properties. MIM is commonly used in various industries such as automotive, aerospace, medical devices, electronics, and consumer products. MIM is typically employed in the production of small metal parts with complex geometries, offering high precision, excellent surface quality, and high mechanical properties.
Metal Injection Molding (MIM) is a process where a feedstock made from metal powders mixed with polymer binders is shaped using the injection molding method, followed by sintering to produce dense, high-performance metal parts. This technology offers significant advantages in the production of small metal parts with complex geometric shapes.
Feedstock Preparation
Metal Powders: High-purity and fine-grained metal powders are used. These powders determine the final density and mechanical properties of the parts.
Binders: Binders such as polymers, wax, and other organic compounds are used to hold the metal powders together.
Mixing and Granulation: Metal powders and binders are mixed to achieve a homogeneous mixture. This mixture is then granulated into a form usable in injection molding machines.
Injection Molding
Molding: The granules are injected into specially designed molds using machines similar to plastic injection machines. At this stage, the parts acquire the desired geometric shape.
Removal from Mold: The injected parts are removed from the mold and have a form called "green part," which is not yet free of binders.
Debinding
Chemical Debinding: Some binders are removed using chemical solvents. During this process, the parts become more porous.
Thermal Debinding: Parts are heated through thermal processes to evaporate the binders. This process is used for complete removal of binders.
Sintering
High-Temperature Heating: The binder-free "brown parts" are subjected to a high-temperature sintering process. Sintering allows the metal powders to fuse and densify.
Furnace Atmosphere: Sintering is usually performed in a protective atmosphere (e.g., vacuum, hydrogen, or inert gas atmosphere), which prevents oxidation and other adverse effects.
Post-Sintering Operations
Thermal Treatments: Additional thermal treatments can be applied to improve the mechanical properties of the parts.
Surface Treatments: Various surface treatments (e.g., coating, polishing) can be applied to enhance the surface quality or for aesthetic purposes.
Machining: If necessary, machining operations may be performed afterward for precise tolerances or additional features.
Complex Geometries: MIM enables the production of metal parts with complex shapes.
High Precision and Repeatability: MIM offers high precision and repeatability, ensuring consistent quality in large-volume productions.
Material Variety: Stainless steel, titanium, nickel-based alloys, and many other metal alloys can be used in the MIM process.
High Mechanical Properties: Parts produced with MIM can have superior mechanical properties compared to casting or machining methods.
Cost Efficiency: Particularly in large-volume productions, MIM provides lower production costs and less material waste.
Automotive Industry: Complex engine parts, gears, and other components requiring high precision.
Aerospace and Defense: Lightweight and durable parts, components requiring high temperature resistance.
Medical Devices: Dental implants, orthopedic implants, and surgical instruments.
Electronics: Small and precise electronic components, connectors, and sensors.
Consumer Products: Eyeglass frames, watch parts, jewelry, and other high-quality consumer products.
The MIM method holds an important place among modern manufacturing technologies, providing innovative solutions in many industries. It enables the production of complex and small metal parts with high quality and low cost, making production processes more efficient.
The features that distinguish Metal Injection Molding (MIM) technology from other metal processing and manufacturing technologies determine its unique advantages and application areas. Here are the main features that highlight MIM technology:
Production of Complex Geometries
MIM enables the production of metal parts with complex shapes and intricate details. Designs that are too complicated to produce with traditional casting, machining, or metal forming methods can be easily manufactured using MIM.
High Precision and Repeatability
MIM offers high precision and repeatability. Produced parts are manufactured within tight tolerance ranges and with consistent quality, which provides a significant advantage in mass production.
Material Variety
MIM is compatible with a wide range of materials. Stainless steel, titanium, nickel-based alloys, copper, and other metal powders can be used to produce parts with various mechanical and chemical properties.
High Mechanical Properties
Parts produced with MIM offer high density and excellent mechanical properties. The sintering process enhances the density of the parts, improving mechanical properties such as strength and durability.
Low Material Waste
MIM minimizes material waste. The injection molding process utilizes a large portion of the material, which increases efficiency. Compared to methods like machining, MIM-produced parts result in less material waste.
High Volume Production
MIM is ideal for high volume production. It offers significant advantages in mass production processes with high production speeds and low part costs.
Surface Quality
Parts produced with MIM offer high surface quality and smoothness. This can reduce or entirely eliminate the need for additional surface treatments.
Reducing the Need for Part Assembly
MIM makes it possible to design complex shaped components that can be produced as a single piece. This increases production efficiency by eliminating processes that require assembly and joining of multiple parts.
High Scalability
MIM can easily scale from small prototypes to large-scale mass production. This provides a significant advantage in product development processes and quick market entry.
Environmental Impact
MIM minimizes environmental impact through energy efficiency and low material waste. Additionally, the recyclability of used materials offers an environmentally friendly production process.
Comparison with Other Technologies
Casting: Casting methods are suitable for large and simple-shaped parts but are limited in producing parts as complex and detailed as MIM. Additionally, casting processes can lead to more material waste and lower surface quality.
Machining: Machining offers high precision but is challenging for producing complex geometries and involves high material waste. MIM provides less material waste and higher efficiency compared to machining.
Metal Forming: Metal forming methods are effective for sheet metal processing but are limited in producing complex three-dimensional parts. MIM offers more flexible and comprehensive solutions in this regard.
Additive Manufacturing (3D Printing): 3D printing is advantageous for prototype production and small-scale productions but is not as economical as MIM for high-volume production. Also, the mechanical properties and surface quality of parts obtained through 3D printing may not be as good as those produced by MIM.
Metal Injection Molding (MIM) technology stands out with its unique advantages in the high-volume production of complex and precise metal parts. These features make MIM a preferred manufacturing method in many industries.