What Are the Durability Features of Flat Bars?
Flat bars are known for their durability features, offering long-lasting use. Here are the key durability features of these bars:
High Tensile Strength: Flat bars have the capacity to bear heavy loads, which is crucial for the safety of structures like bridges and high-rise buildings.
Corrosion Resistance: Flat bar types produced with galvanized coating or special alloys show high resistance to rust, providing a significant advantage for outdoor applications.
Thermal Resistance: Flat bars that can withstand high temperatures are highlighted as a reliable option in industrial facilities and the energy sector.
Easy Shaping: With their flexible structure, flat bars can be easily shaped to meet various design and use requirements.
How Are the Different Sizes of Flat Bars Determined?
The sizes of flat bars are determined based on the area of use and the required load-bearing capacity. Besides standard production sizes, customized sizes for special projects are also possible. The following factors influence size determination:
Cross-section Dimensions: Flat bar varieties are typically produced in cross-sections ranging from 20x3 mm to 200x20 mm.
Length: Flat bars are typically produced in lengths of 6 meters or 12 meters, but they can also be offered in different sizes to meet project requirements.
Thickness: The choice of thickness depends on the load the material will carry and the environment in which it will be used. Thinner flat bars are preferred for decorative purposes, while thicker ones are used in projects with high load-bearing capacity.
What Materials Are Flat Bars Made From?
Flat bars are generally made from carbon steel or alloy steel materials. The material used in production directly affects the durability, flexibility, and corrosion resistance of the bar. Here are the most commonly used materials:
Carbon Steel: Carbon steel, the most preferred material, stands out with its solid structure and affordable cost. Different carbon content levels determine the hardness and durability characteristics of the bar.
Galvanized Coating: Galvanized coating is applied to flat bar types intended for outdoor use, providing extra protection against rust.
Stainless Steel: A more durable and long-lasting material, stainless steel is especially preferred in decorative and industrial applications.
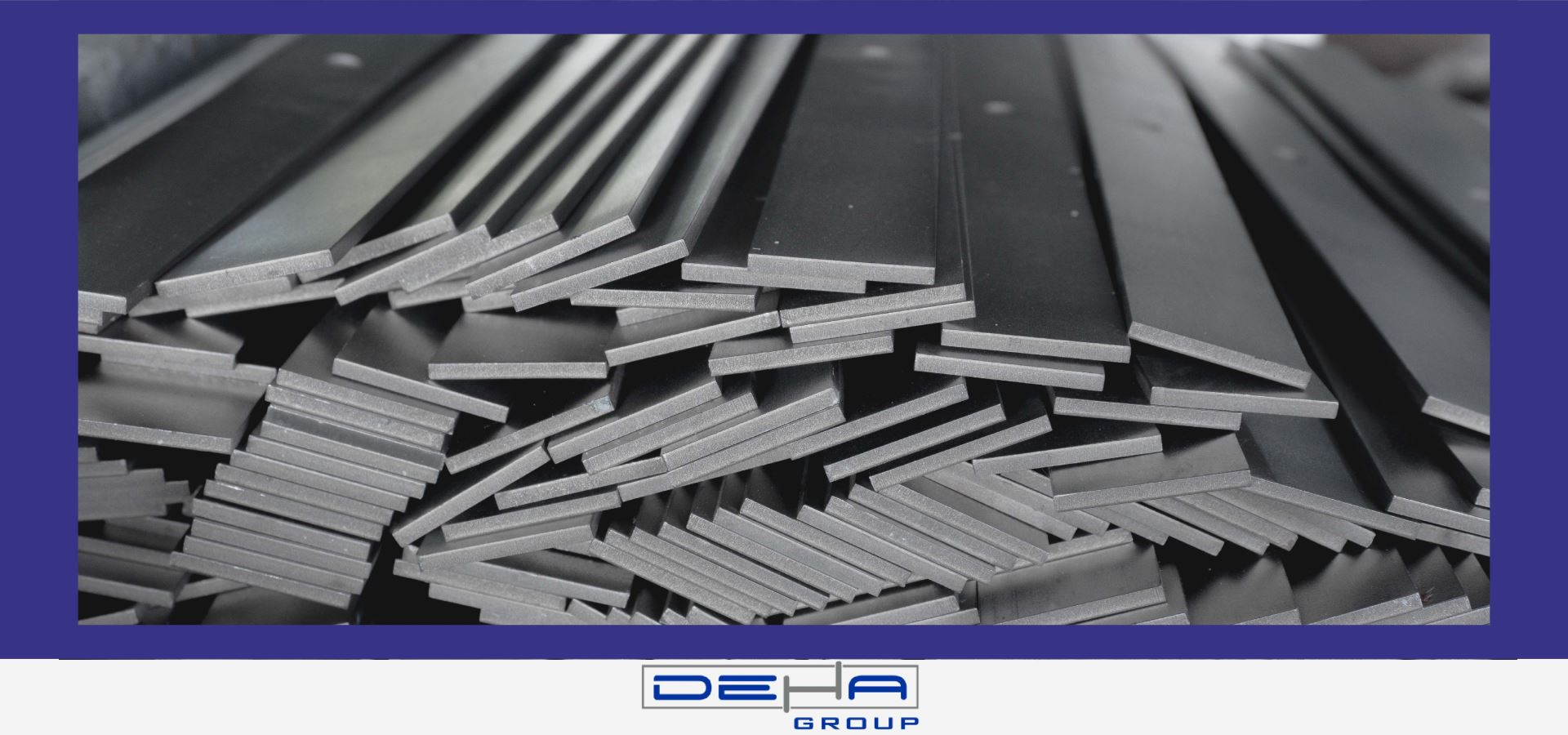
What Should Be Considered During the Installation of Flat Bars?
Flat bars are a crucial material type widely used in the construction industry. There are a few key points to consider during installation. First, it must be ensured before installation that the dimensions and quality of the flat bars to be used comply with the project requirements. Flat bars should be cut to the correct dimensions, and if welding is involved, welding processes should be carried out according to standards.
During installation, care should be taken to ensure that surfaces are clean. Issues like rust or surface contamination can negatively affect the solidity and longevity of the installation. Furthermore, appropriate connection elements should be used during the installation of flat bars, and attention should be paid to the quality of these elements. Regardless of whether screwing, riveting, or welding is preferred, safety standards and engineering calculations should be considered.
What Are the Most Used Coating Types for Flat Bars?
Flat bars are treated with various coating methods to enhance their durability when exposed to environmental conditions and protect them against corrosion. One of the most preferred coating types is galvanizing. In this method, flat bars are coated with zinc to provide resistance against rust. Galvanized coating is ideal for flat bars used outdoors because it provides long-lasting protection against humidity, rain, and other natural factors.
Another common coating method is electrostatic powder coating. In this method, the surface of the flat bars is coated with powder paint and baked to achieve a hard surface. Powder coating offers both aesthetic appeal and protection against environmental factors.
Epoxy coating is another preferred method for flat bars. Epoxy coatings are highly resistant to water and chemicals, making them widely used in industrial areas. When choosing a coating method, the area of use and environmental factors should be considered. The quality and lifespan of the coating are critical for making the right choice among flat bar varieties.
How Resistant Are Flat Bars to Environmental Conditions?
The resistance of flat bars to environmental conditions depends on the quality of the material and the type of coating applied. Flat bars made from stainless steel are naturally more resistant to corrosion and withstand most environmental factors. However, standard carbon steel flat bars can rust quickly in humid environments if uncoated.
Durability against environmental conditions can be enhanced with protective measures like galvanizing or epoxy coating. For example, the use of galvanized coating on flat bars in outdoor environments ensures long-term reliable use without being affected by factors like humidity, rain, and snow.
It should be noted that if the right material and coating method are not selected for resistance to environmental conditions, flat bar varieties can quickly undergo deformation. Therefore, proper planning suitable for the intended use is important.
According to Which Standards Are Flat Bars Produced?
Flat bars are produced in compliance with national and international steel standards. In Turkey, TSE (Turkish Standards Institute) standards are generally based on, while ASTM (American Society for Testing and Materials) and EN (European Norms) standards are commonly used internationally. These standards define the dimensions, strength, and mechanical properties of flat bars.
Standards play a critical role in determining which applications certain flat bar types are suitable for. For instance, specific durability and tensile strength may be required for flat bars used in building steel frames. Similarly, weldability is also included within the scope of standards.
Ensuring that flat bars are produced according to standards is crucial for both structural safety and extending the lifespan of the material. It should not be forgotten that a flat bar that complies with international standards offers high quality and reliability.
What Are the Differences Between Flat Bars and Profiles?
Flat bars and profiles are materials commonly used in steel structures and industrial applications. However, there are distinct differences between these two materials.
Flat bars are typically flat and rectangular in shape. Profiles are usually produced as T profiles, U profiles, I profiles, or H profiles. Flat bars have a simpler design and are often used as connecting elements or support structures. Profiles, on the other hand, are used as main load-bearing elements in more complex structures.
Another difference is seen in durability and tensile strength. Profiles generally have a higher capacity for carrying heavier loads. However, flat bars are a more suitable option for applications requiring fine detail solutions. Flat bar varieties can be lighter than profiles, which provides an advantage in certain applications.
There are also differences in terms of production costs and applicability. Flat bars are generally a more economical option and are easier to install. However, the required load-bearing capacity in a project may necessitate the use of profiles. The advantages and disadvantages of both materials should be considered to choose solutions appropriate for project characteristics.