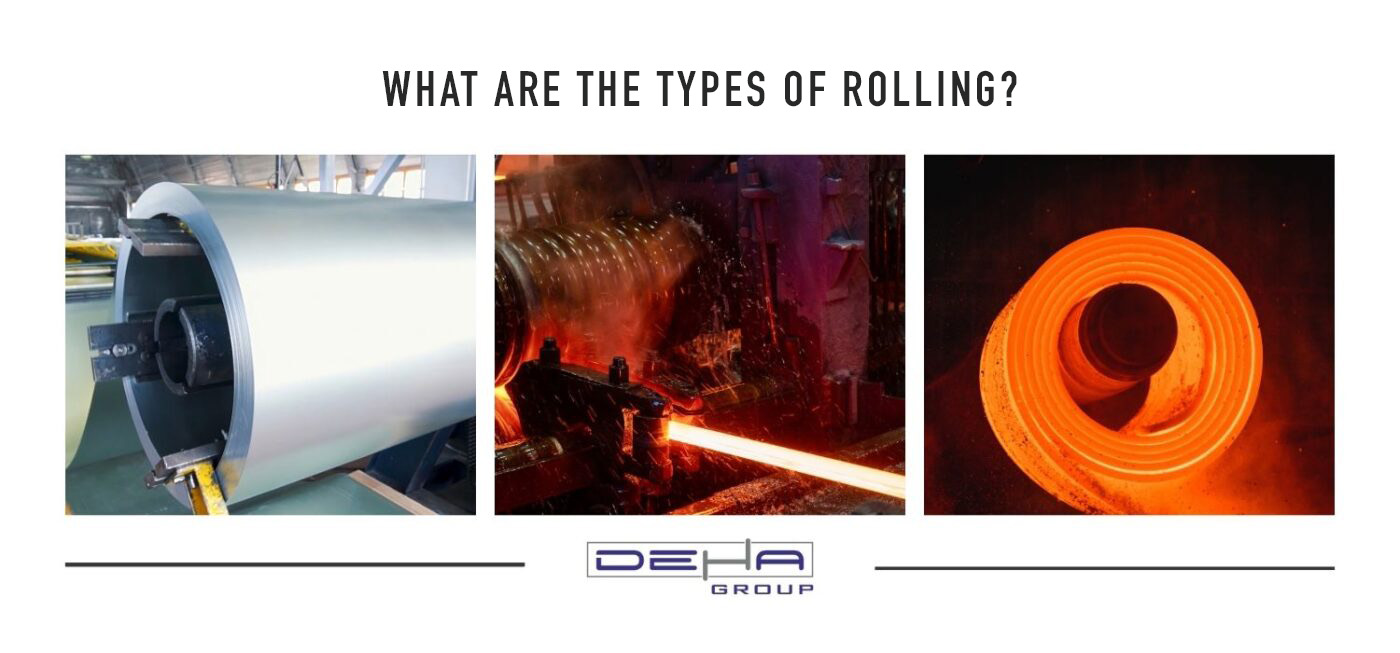
Rolling is the process of compressing metals between cylinders to obtain a specific thickness and shape. This process helps the metal take on the desired shape and improves its mechanical properties. The rolling process is divided into two main categories: hot rolling and cold rolling.
Hot rolling is a method of processing metal at high temperatures. The temperature of the metal is below its melting point, but still at a high level. During this process, the fluidity properties of the metal increase, allowing it to be shaped and processed more easily. This method helps reduce irregularities in the crystalline structure within the metal, resulting in a more homogeneous structure. Hot rolling is commonly applied to metals such as steel, aluminum, and copper.
Hot Rolling Process
Heating: The metal block or ingot is heated to a certain temperature before the hot rolling process. This temperature typically ranges between 60% to 80% of the metal's melting temperature. For instance, for steel, this temperature can be approximately 1100-1250°C. Heating facilitates the plastic deformation of the metal, enhancing its ability to take shape.
Rolling: The heated metal is passed between two or more cylinders. These cylinders rotate and apply force to the metal, reducing its thickness and increasing its width. The rolling cylinders enable the production of metal in desired shapes and sizes.
Cooling: After the rolling process is completed, the metal is usually cooled in a controlled manner. This cooling process aims to organize the crystalline structure of the metal and achieve the desired mechanical properties. Cooling may be carried out using various methods, such as natural air cooling or water cooling.
Advantages of Hot Rolling
Workability: High temperatures increase the metal’s ability to take shape. As the fluidity of the metal increases, products with more complex and fine details can be produced.
Internal Structure Improvement: Hot rolling reduces irregularities in the metal’s crystalline structure, providing a more homogeneous structure. This improves the mechanical properties and durability of the metal.
Large Product Sizes: Hot rolling allows for the production of large-diameter and long-length products. This is especially important for large profiles and pipes used in the construction sector.
Cost Efficiency: Hot rolling allows for the fast processing of large quantities of metal. This can reduce production costs and make the production process more efficient.
Applications of Hot Rolling
Construction Industry: Large steel profiles, beams, columns, and other structural elements are often produced using hot rolling.
Automotive Industry: Vehicle body panels, chassis components, and other metal parts are shaped using hot rolling.
Energy Sector: Hot rolling is frequently used in the production of pipes and profiles. Especially pipes and connection elements required for the energy sector are produced with this method.
Methods of Hot Rolling
Horizontal Rolling: The metal is processed between horizontal cylinders. This method is typically used in the production of large metal sheets and strips.
Vertical Rolling: The metal is processed between vertical cylinders. This method is usually preferred in the production of pipes and profiles.
Hot rolling not only enhances the formability and workability of metal but also enables the production of large-sized, durable products. This method offers a wide range of applications in various industries.
Cold rolling is the process of working metal at a temperature close to room temperature. During this process, the metal's temperature is well below its melting point and is usually near or slightly above room temperature. Cold rolling allows for shaping the metal in a thinner and more precise manner. It also enhances the mechanical properties, surface quality, and durability of the metal. Cold rolling is used especially in the production of thin sheets, strips, and parts requiring high precision.
Cold Rolling Process
Pre-Heating (If Necessary): Cold rolling generally does not require the metal to be pre-heated. However, in some cases, low-level pre-heating might be done to ensure better shaping of the metal.
Rolling: The metal is passed through two or more rotating rollers while cold. These rollers reduce the thickness and increase the width of the metal. The forces applied during cold rolling compress the crystal structure of the metal, allowing it to take shape.
Surface Treatments: Any roughness and defects that may occur on the metal surface during cold rolling are usually corrected with additional surface treatments. These may include sanding, polishing, and coating processes.
Cooling and Final Treatments: After the rolling process is completed, the metal is usually cooled in a controlled environment. The cooling process is crucial for improving the metal's crystal structure and final physical properties. Additionally, the final shape and dimensions of the metal are verified and corrected with additional processing steps.
Advantages of Cold Rolling
Thin and Precise Shaping: Cold rolling allows the metal to be processed in very thin and precise dimensions. This is a great advantage for the production of products requiring high tolerance.
Surface Quality: The cold rolling process enhances the surface quality of the metal. Surface roughness is reduced, resulting in a smoother surface, which can be important for both aesthetic and functional reasons.
Mechanical Properties: Cold rolling increases the strength and hardness of the metal. During the process, the crystal structure of the metal is compressed, thus improving its mechanical properties.
Small Production Quantities: Cold rolling is suitable for small production batches and allows for the rapid production of products requiring high precision.
Applications of Cold Rolling
Automotive Industry: Thin and precise metal parts are used as chassis components, engine parts, and other components in the automotive sector.
Electronics Industry: Thin metal sheets and connectors used in electronic devices are produced by cold rolling.
Packaging: Metal packaging materials, especially thin and durable strips and sheets, are produced by cold rolling.
Cold Rolling Methods
Strip Rolling: Used to produce metal strips of a certain width and thickness. These strips are widely used in the automotive and electronics industries.
Sheet Rolling: Metal sheets are obtained with smooth and flat surfaces through cold rolling. These sheets are used for various applications in different industries.
Cold Rolling of Pipes: Metal pipes are produced with thin walls and high precision through cold rolling. These pipes are commonly used in the automotive and construction sectors.
Disadvantages of the Cold Rolling Process
High Energy Consumption: The cold rolling process requires the metal to be processed with high energy, which can increase energy costs.
Processing Limitations: Some metals can be difficult to process during the cold rolling process, leading to processing limitations.
Cold rolling is an ideal method for metalworking applications requiring high precision and surface quality. This process can be used in various industrial applications by increasing the mechanical properties and durability of the metal.
Continuous rolling is a method of rolling that allows metal strips or sheets to be processed in a continuous production line. This method enables the metal to be continuously shaped and generally ensures the rapid and efficient production of large quantities of products. Continuous rolling is an advanced technology used in the metal processing industry to provide high efficiency, consistency, and low cost.
Continuous Rolling Process
Ingot or Semi-Finished Production
The continuous rolling process usually starts with the metal in the form of an ingot or semi-finished product. This semi-finished product consists of metal blocks or strips obtained through methods such as hot rolling or casting.
The temperature and shape of the metal are optimized for subsequent processing stages.
Heating
Metal strips are heated before entering the continuous rolling line. This heating is done to increase the fluidity and workability of the metal.
Heating is usually done using methods such as induction furnaces or gas furnaces, and the metal's temperature is brought to a suitable level for the rolling process.
Continuous Rolling Line
The metal strip is passed through a series of rotating cylinders in the continuous rolling line. These cylinders shape the metal to the desired thickness and width.
The continuous rolling line typically includes a series of rolling machines, cooling units, and control systems. These systems ensure the continuous processing of the metal and guarantee the high quality of the final product.
Cooling
The metal strip is cooled in a controlled manner during and after the rolling process. This cooling process is crucial for regulating the mechanical properties and crystal structure of the metal.
Cooling is usually done with water or air and can affect the surface quality of the metal.
Final Processes
After the rolling and cooling processes, the metal strip is usually subjected to additional processing steps. These processes include surface cleaning, cutting, coating, and quality control.
Metal strips are often cut into specific sizes and packaged.
Advantages of Continuous Rolling
High Efficiency: Continuous rolling allows for uninterrupted processing of the metal. This accelerates the production process and allows for the rapid production of large quantities of products.
Low Cost: Continuous rolling can reduce costs due to high-volume production. Continuous processing optimizes labor and energy costs.
Product Quality: Continuous rolling ensures homogeneous processing of the metal. This guarantees the high quality and consistency of the products.
High Accuracy and Tolerance: Continuous rolling allows the metal to be processed with high precision. This helps in obtaining high-quality products with narrow tolerances.
Low Waste: Continuous rolling converts almost all of the metal into the product, thus minimizing material waste.
Applications of Continuous Rolling
Automotive Industry: Automotive parts and chassis components require high precision and durability. Continuous rolling ensures the high-volume production of such products.
Packaging: Metal packaging materials, especially thin and durable strips, are produced with continuous rolling. These materials are used in packaging food and other products.
Construction Sector: Metal profiles and steel structural elements used in the construction sector are produced through continuous rolling. This allows for obtaining large-sized products with high durability.
Energy Sector: In the energy sector, pipes and other metal components are produced through continuous rolling. This provides high efficiency and durability.
Continuous Rolling Methods
Strip Rolling: Obtained by the continuous processing of metal strips. These strips are used in the automotive and packaging sectors.
Sheet Rolling: Allows the continuous processing of wider metal sheets. These sheets are used in various industries.
Breakdown Rolling: Used to reduce the thickness and increase the width of the metal. This method is particularly common in the iron and steel industries.
Continuous Pipe Rolling: Obtained by continuously processing metal pipes. These pipes are used in the energy and construction sectors.
Continuous rolling is an essential method in the metal processing industry for enhancing efficiency, cost control, and product quality. This process provides the production of high-volume and consistent products for various industrial applications.
Breakdown rolling is a metal processing method used to increase the width of a metal while reducing its thickness. In this method, the metal is passed between two rotating cylinders, which apply force to the metal, allowing it to be shaped. Breakdown rolling can process metal in longitudinal (horizontal) or transverse (vertical) directions and is commonly used in the iron and steel industries.
Breakdown Rolling Process
Preparation of Metal Material
The metal to be used in the process should first be prepared in the desired shape and size, either in an ingot or semi-finished form. This material must be brought to the appropriate temperature before hot or cold rolling.
Heating (For Hot Rolling)
If hot rolling is to be applied, the metal material is heated to a high temperature. This makes it easier for the metal to be shaped. Heating is usually done in a furnace or induction device.
Rolling Process
The metal is passed between two or more rotating cylinders. These cylinders apply pressure to the metal, reducing its thickness and increasing its width. The motion of the cylinders controls the shaping process of the metal.
Cylinders are typically designed to be smooth, cylindrical, and rotational. The movement of these cylinders ensures the continuous processing of the metal.
Process Parameters
Gap Between Cylinders: The gap between the cylinders is adjusted to reduce the thickness of the metal during processing. This gap determines how thick or thin the metal will be.
Cylinder Speed: The rotation speed of the cylinders affects the processing speed of the metal. This speed determines how quickly the metal will be shaped.
Pressure and Force: The force applied to the cylinders affects the shaping capability and thickness of the metal. This force ensures the metal is shaped consistently.
Cooling and Final Processes
After the rolling process is completed, the metal is usually cooled in a controlled manner. This cooling process is important to improve the crystal structure and mechanical properties of the metal.
The metal can then undergo additional processing steps, including surface cleaning, cutting, polishing, and coating.
Advantages of Breakdown Rolling
Fast Production: Breakdown rolling allows for fast processing of metal, enabling the production of a large quantity of products in a short time.
Large Sizes: This method is suitable for the production of large-scale metal products. It is used particularly in the construction and automotive industries for producing large metal profiles and pipes.
Homogeneous Product Quality: Breakdown rolling ensures that the metal is processed homogeneously, enhancing product quality control and consistency.
Cost Efficiency: By offering a continuous production process, it optimizes labor and energy costs, potentially reducing costs in large volume productions.
Improved Mechanical Properties: The stresses and rearrangements in the crystal structure during the shaping of the metal improve the mechanical properties of the product.
Applications of Breakdown Rolling
Construction Industry
Large steel profiles, beams, and columns are typically produced using the breakdown rolling method. These products are used in construction projects requiring high durability and large dimensions.
Automotive Industry
Large metal parts, chassis components, and pipes used in the automotive sector are produced via breakdown rolling, providing high durability and safety.
Energy Sector
Pipes and other metal parts for the energy sector are produced using breakdown rolling. These parts are used in applications like power transmission lines and power plants.
Methods of Breakdown Rolling
Horizontal Breakdown Rolling
The metal is passed between horizontally rotating cylinders. This method is generally used for the production of metal sheets and strips.
Vertical Breakdown Rolling
The metal is passed between vertically rotating cylinders. This method is preferred for pipe and profile production.
Double-Vertical Breakdown Rolling
The metal is processed in a system with both horizontal and vertical cylinders. This method is used for producing more complex shapes and dimensions.
Disadvantages of Breakdown Rolling
High Energy Consumption: Breakdown rolling requires high energy to shape the metal, which can increase energy costs.
Processing Limitations: Some metals can be difficult to process during breakdown rolling, leading to workability restrictions.
Surface Quality: Surface roughness can occur on the metal during breakdown rolling, necessitating additional surface treatments.
Breakdown rolling allows for rapid and efficient shaping of metal, enabling the production of large-sized and durable products. This method offers a wide range of applications for various industrial applications.