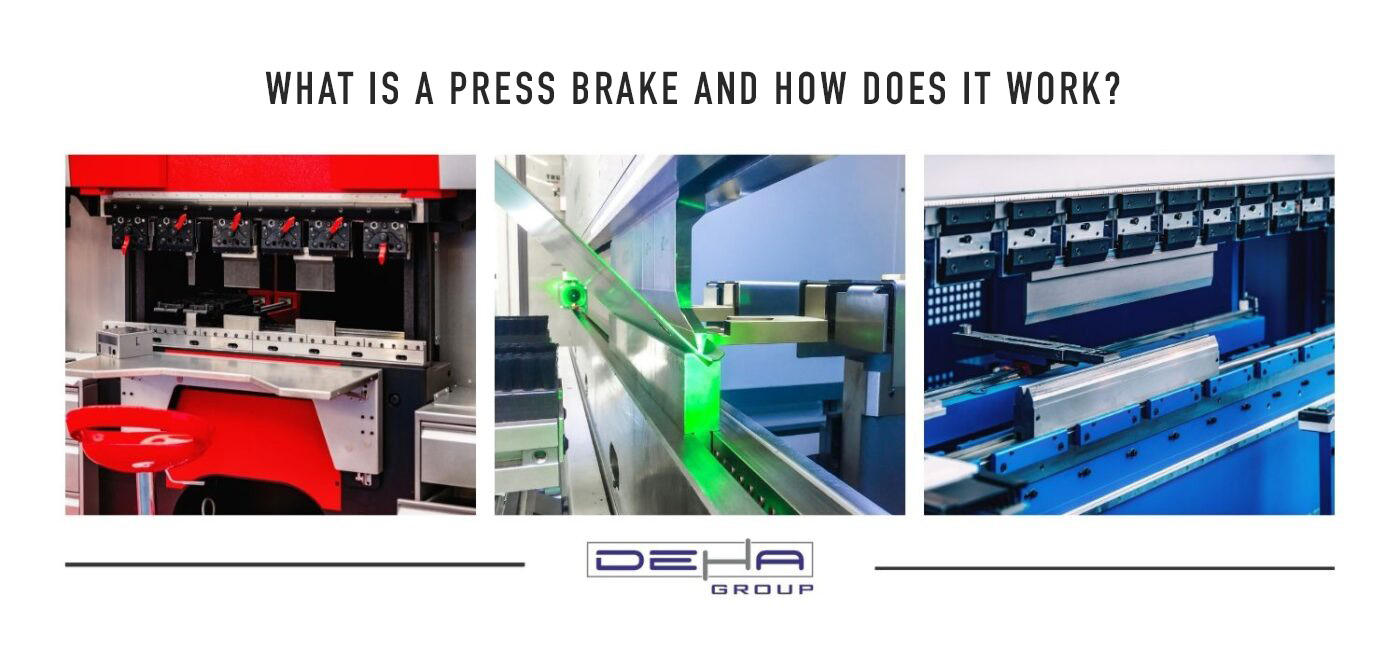
The press brake is a processing machine used for bending metal sheets at specific angles. This machine consists of two main components: the upper and lower jaws. The sheet metal is placed between these two jaws, and the upper jaw ensures that the metal is bent at the desired angle. Press brakes are particularly used in the production of metal body parts, industrial equipment, and structural elements.
Modern press brakes are usually equipped with CNC (Computer Numerical Control) systems, which allow bending operations to be carried out with high precision and repeatability. This feature makes it possible to achieve accurate and effective results in various metal processing applications.
Bending Capacity: Press brakes have several important factors that determine the bending capacities of sheet metals. These factors include the machine's bending length, the thickness of the sheet, and the bending angle. The machine typically has the capacity to bend sheet thicknesses ranging from a few millimeters to a few centimeters. The bending length determines how wide a sheet the machine can process.
Jaw Structure and Design: Press brakes consist of two main components: the upper jaw (punch) and the lower jaw (die). The upper jaw provides the force applied to the metal sheet during the bending process. The lower jaw is the section where the metal sheet is supported and made ready for bending. The jaws are usually interchangeable and can have various designs for bending different shapes and angles.
Control Systems: Modern press brakes are equipped with CNC (Computer Numerical Control) systems. These systems allow the machine to perform bending operations with high precision. CNC control makes it possible to program bending angles, depths, and other parameters, ensuring repeatable and high-quality results.
Bending Angle and Depth Adjustments: Press brakes have the ability to precisely adjust bending angles. Bending angles typically range from 0 to 180 degrees. Additionally, the bending depth is adjustable, which determines how much the metal needs to be bent to achieve the desired shape.
Speed and Efficiency: Press brakes can operate at high speed and efficiency. This saves time and labor in the production process. Machine operators can make various adjustments to optimize speed and efficiency, providing a significant advantage in large-scale production.
Precision and Repeatability: Thanks to CNC control systems, press brakes offer a high degree of precision and repeatability. This is especially important in the production of high quantities and complex metal parts. Each bending operation is automatically performed according to programmed parameters, minimizing the error rate.
These features allow press brakes to be used effectively and efficiently in various metalworking applications.
The areas of use for press brakes are quite extensive and they are widely used in various industries. Here are the main areas where press brakes are utilized:
Automotive Industry: Press brakes are frequently used in the automotive sector for the production of metal body parts. They are ideal for the precise bending of components such as vehicle bodies, door panels, and frame elements.
Construction and Building Industry: Press brakes play an important role in the production of building elements such as metal frames, support structures, and exterior claddings. They are used particularly for shaping the metal parts required for large buildings and industrial structures.
Machinery and Equipment Manufacturing: Press brakes are used in the production of machine and equipment parts, particularly for bending components like metal cases, enclosures, and support structures. This is a critical step in the production of various industrial machines and equipment.
Furniture and Interior Design: Press brakes are also used in the production of metal furniture parts, decorative elements, and interior design components. Metal shelves, table legs, and other decorative objects can be processed with this machine.
Electrical and Electronics Industry: Press brakes are used in the production of electrical panels, enclosures, and other electronic equipment parts. Precise and correct bending of these parts is important for functionality and safety.
Industry and Industrial Production: Press brakes are used in the industrial sector for the production of various metal parts. In industrial production, components of various machines and production lines are shaped using press brakes.
Recycling and Waste Management: Press brakes are also used in applications where metal sheets need to be bent properly during the processing and recycling of metal waste.
This wide range of uses highlights the importance and versatility of press brakes in the metalworking industry.
The working principle of the press brake is based on the bending of metal sheets at a certain angle. This process consists of several basic stages, and each stage requires high precision and control. Here are the working principle and stages of the press brake:
Preparation Stage
Sheet Placement: The metal sheet is carefully placed on the lower table of the press brake. Correct positioning of the sheet is critically important for the precision of the bending process.
Die Selection: Suitable dies are selected for the bending process. Dies ensure that the metal sheet is bent at the desired angle and shape. Typically, two main dies are used: the upper die (punch) and the lower die (die).
Adjustment Stage
Angle and Depth Adjustment: The bending angle and depth are adjusted via the control panel of the press. These adjustments ensure that the metal sheet is bent at the correct angle and depth. Modern press brakes are equipped with CNC (Computer Numerical Control) systems that can automatically make these adjustments.
The working principle of the press brake is based on the bending of metal sheets at a certain angle. This process consists of several basic stages, and each stage requires high precision and control. Here are the working principle and stages of the press brake:
Preparation Stage
Sheet Placement: The metal sheet is carefully placed on the lower table of the press brake. Correct positioning of the sheet is critically important for the precision of the bending process.
Die Selection: Suitable dies are selected for the bending process. Dies ensure that the metal sheet is bent at the desired angle and shape. Typically, two main dies are used: the upper die (punch) and the lower die (die).
Adjustment Stage
Angle and Depth Adjustment: The bending angle and depth are adjusted via the control panel of the press. These adjustments ensure that the metal sheet is bent at the correct angle and depth. Modern press brakes are equipped with CNC (Computer Numerical Control) systems that can automatically make these adjustments.