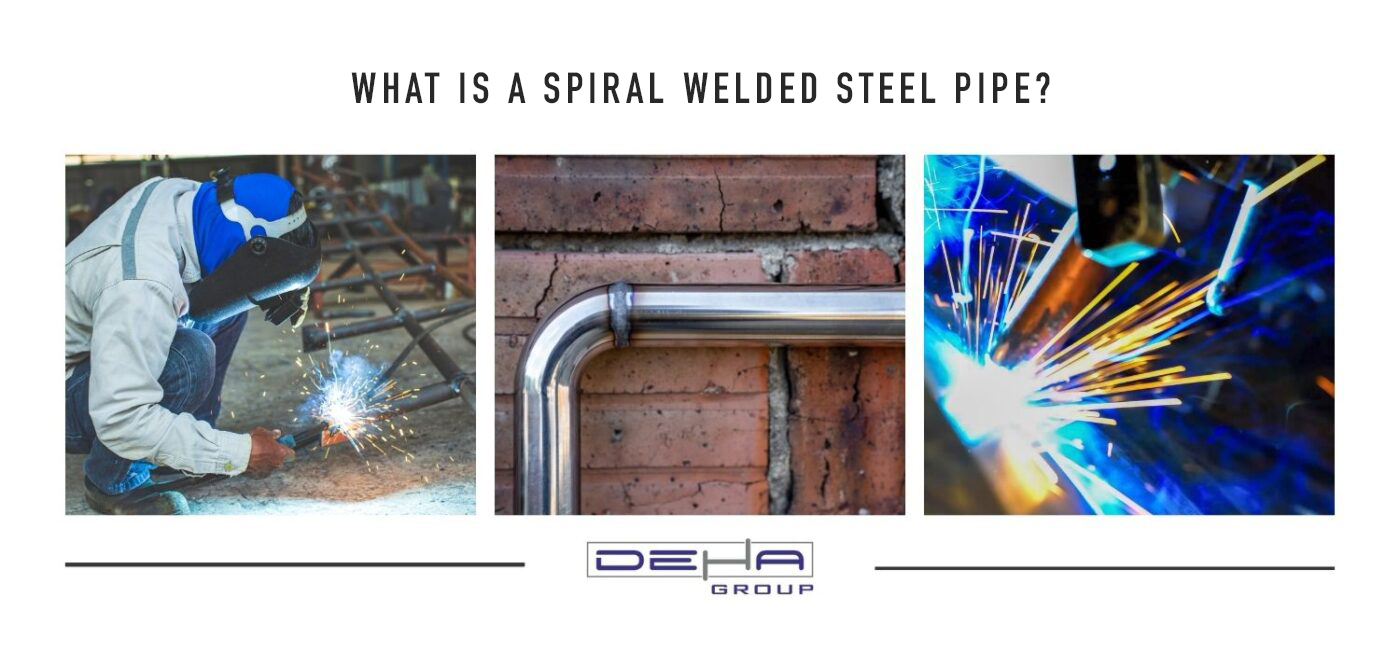
Spiral welded steel pipes are a type of pipe produced by spirally bending and welding steel plates. This production method allows for the manufacture of pipes with larger diameters and lengths. Compared to other types of steel pipes, spiral welded pipes have a more economical production process and are preferred in projects requiring large diameter pipelines. These pipes are known for their resistance to high pressure and external factors.
Spiral welded steel pipes are commonly used in infrastructure projects such as oil, natural gas, water, and wastewater lines. The quality of the material used in the production of the pipes directly affects the pipe's service life and performance. Spiral pipes produced with high-quality steel material offer long-lasting use and show resistance to corrosion. Additionally, the techniques used during the welding process enhance the pipe's strength, increasing its pressure resistance.
Another advantage of spiral welded steel pipes is their ability to be produced in different diameters and lengths during manufacturing. This flexibility makes it easier for them to adapt to various projects. Furthermore, the wall thickness of the pipes can be adjusted according to requirements during production. Thus, thicker-walled pipes are preferred for lines exposed to high pressure, while thinner-walled pipes are used in projects requiring lower pressure.
Spiral welded steel pipes have a wide range of uses in many different industries. They are particularly preferred in infrastructure projects for the construction of water, oil, and natural gas lines. Due to their high durability, they are very effective against harsh environmental conditions and high-pressure fluid transmission processes. Therefore, they are widely used in long-distance pipelines.
Additionally, spiral pipes are also used in various construction projects such as underwater pipelines, bridge construction projects, and building foundation reinforcement works. Civil engineers aim to enhance safety and durability by using these pipes in large-scale structural projects. The flexible manufacturing possibilities of the pipes allow for custom solutions tailored to different needs, making them indispensable in the construction sector.
Lastly, spiral welded steel pipes also hold an important place in the energy sector. They are used as steam pipes in power plants and are part of various applications in renewable energy projects. The long lifespan of these pipes reduces the costs of energy projects while keeping maintenance requirements to a minimum.
Spiral welded steel pipes differ from straight seam welded pipes. Straight seam pipes are made by joining and welding the edges of a flat sheet, which is suitable for smaller diameter pipes. However, spiral welded pipes are produced by bending the sheet in a spiral form, allowing the production of larger diameters. This feature makes spiral pipes the preferred choice in projects requiring large diameter pipelines.
Additionally, the production process of spiral welded pipes is faster and more economical compared to straight seam pipes. The weld seam of spiral pipes continues spirally along the entire circumference of the pipe, which results in a more even load distribution and enhances the overall strength of the pipe. This makes spiral pipes more resistant to pressure. Since weak points can occur along the weld line in straight seam pipes, opting for spiral pipes in such projects can be more advantageous in terms of safety.
In conclusion, the advantages of large diameter production, cost-effectiveness, and pressure resistance of spiral welded pipes make them more preferable over straight seam pipes for certain projects. The ability to manufacture these pipes to meet different needs supports their versatile application areas.
One of the biggest advantages of spiral welded steel pipes is the low production cost. The spiral bending method allows for efficient use of the sheet, enabling pipes to be economically produced in larger diameters and lengths. Additionally, the welding methods used in the production of spiral pipes enhance their durability, making them long-lasting in pressurized and challenging environments.
However, there are also some disadvantages to spiral welded steel pipes. For example, in high-pressure and critical applications, they may require more meticulous quality control processes compared to straight seam pipes. Small defects that can occur along the spiral weld lines may adversely affect the pipe's durability. Therefore, spiral pipes need to be rigorously tested before being used, especially in high-pressure lines.
In conclusion, while spiral welded steel pipes stand out in large-scale projects due to the flexibility and cost advantages they offer, careful evaluation in specific applications and the implementation of appropriate quality control processes are necessary.