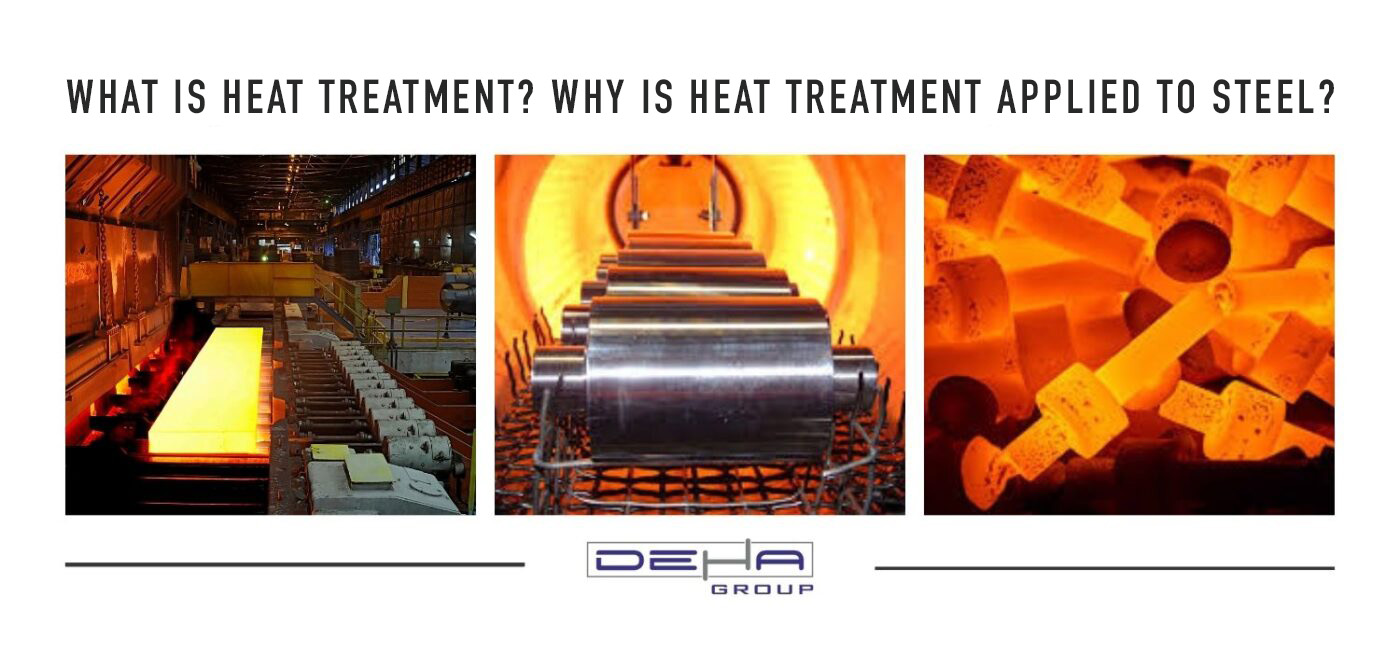
Heat treatment is the controlled process of heating and cooling metals and alloys to change their mechanical and physical properties. This process imparts desired characteristics such as hardness, durability, ductility, and toughness to the metals. Heat treatment enhances performance and lifespan by altering the metal's crystal structure and microstructure. It is commonly used in various industries such as automotive, aerospace, machinery manufacturing, and construction.
Heat treatment is a thermal process performed to enhance the mechanical properties and durability of metal parts or to achieve desired characteristics. The main reasons are as follows:
Improvement of Mechanical Properties: Heat treatment can increase a metal's hardness, strength, durability, and wear resistance. For example, the hardness or ductility of steels can be controlled through heat treatment methods.
Enhancement of Machinability: Some heat treatment methods improve the machinability of metal, allowing for easier shaping during processing.
Improvement of Surface Properties: Heat treatment can enhance the metal surface's resistance to corrosive effects, wear, or fatigue, which can extend the component's lifespan.
Microstructure Control: Heat treatment can alter the metal's microstructure to correct undesired properties or provide desired structural characteristics. This is one of the factors determining the material's performance.
High-Temperature Applications: Some industrial applications require components to operate at high temperatures. Heat treatment can increase or adapt the resistance to such conditions.
Heat treatments are an important technique widely used in the metalworking industry, and when applied correctly, they can significantly enhance material performance.
The heat treatment process generally consists of three main stages: heating, annealing, and cooling. These stages vary depending on the type of material, the desired properties, and the process to be applied.
Heating: The first stage of heat treatment is the heating of the metal to a certain temperature. This temperature should be carefully selected based on the type of material and the desired mechanical properties. During the heating process, the temperature must be distributed evenly and increased at a controlled rate. Otherwise, undesired stresses and cracks may form in the structure of the metal. Another important point to consider during the heating stage is the control of the atmosphere. Inert gases or a vacuum environment can be used to prevent oxidation and other chemical reactions.
Annealing: The second stage of heat treatment, annealing, involves holding the metal at a certain temperature for a specific period. This process reduces the internal stresses of the metal, resulting in a more homogeneous structure. The annealing time and temperature should be carefully adjusted according to the thickness of the material and the desired properties. During the annealing process, significant changes occur in the microstructure of the metal. Crystal grains grow, reducing internal stresses and improving the workability of the metal. Annealing allows for easier shaping and processing of the metal.
Cooling: After the annealing stage, the metal is cooled at a specific rate. The cooling rate determines the microstructure and mechanical properties of the metal. Rapid cooling (quenching) increases the hardness of the metal, while slow cooling results in a structure with more ductile and tough properties. The most important factor to consider during the cooling process is the uniform cooling of the metal. Sudden and uneven cooling can cause cracks and internal stresses in the metal structure. Therefore, the cooling medium and method should be carefully selected.
Heat treatment can be applied with different purposes and methods. The main types of heat treatment are as follows:
Annealing: Annealing is a heat treatment process performed to soften the metal, relieve internal stresses, and improve machinability. During annealing, the metal is heated to a specific temperature and held at this temperature for a certain period. It is then cooled slowly. Annealing eliminates irregularities in the metal’s internal structure and makes the crystal structure homogeneous.
Normalizing: Normalizing is a heat treatment process performed to homogenize the microstructure of the metal and improve its mechanical properties. During normalizing, the metal is heated above the critical temperature and then cooled in air. This process refines the grain structure of the metal, resulting in a more homogeneous structure.
Hardening: Hardening is a heat treatment process performed to increase the hardness and wear resistance of the metal. During hardening, the metal is heated above the critical temperature and then rapidly cooled. This rapid cooling process ensures that the metal gains hardness. However, after hardening, the metal's brittleness increases and therefore tempering may be applied.
Tempering: Tempering is a heat treatment process performed to reduce the brittleness of hardened metal and increase its toughness. During tempering, the hardened metal is heated to a specific temperature and held at this temperature for a certain period. It is then cooled slowly. Tempering optimizes the balance between hardness and toughness of the metal.
Heat treatment plays a critical role in the metal processing industry and, when applied correctly, provides significant improvements in material properties. Heat treatment processes make metals more durable, hard, ductile, and workable. These features make metals suitable for various industrial applications. For example, processes such as the hardening of engine parts in the automotive industry, the tempering of aircraft bodies in the aviation industry, and the normalization of steel constructions in the construction sector are some of the common uses of heat treatment.
Heat treatment also eliminates defects in the internal structure of the metal and increases the material's homogeneity. This ensures that the metal is more reliable and long-lasting. The correct application of heat treatment processes ensures the production of high-quality and high-performance products in the metal processing industry.
Heat treatment is an important technique used to give metals and alloys the desired mechanical and physical properties. Heat treatment processes improve characteristics such as hardness, durability, ductility, and toughness by altering the metal's crystal and microstructure. This enhances the performance of the metal and allows for more efficient use in industrial applications.