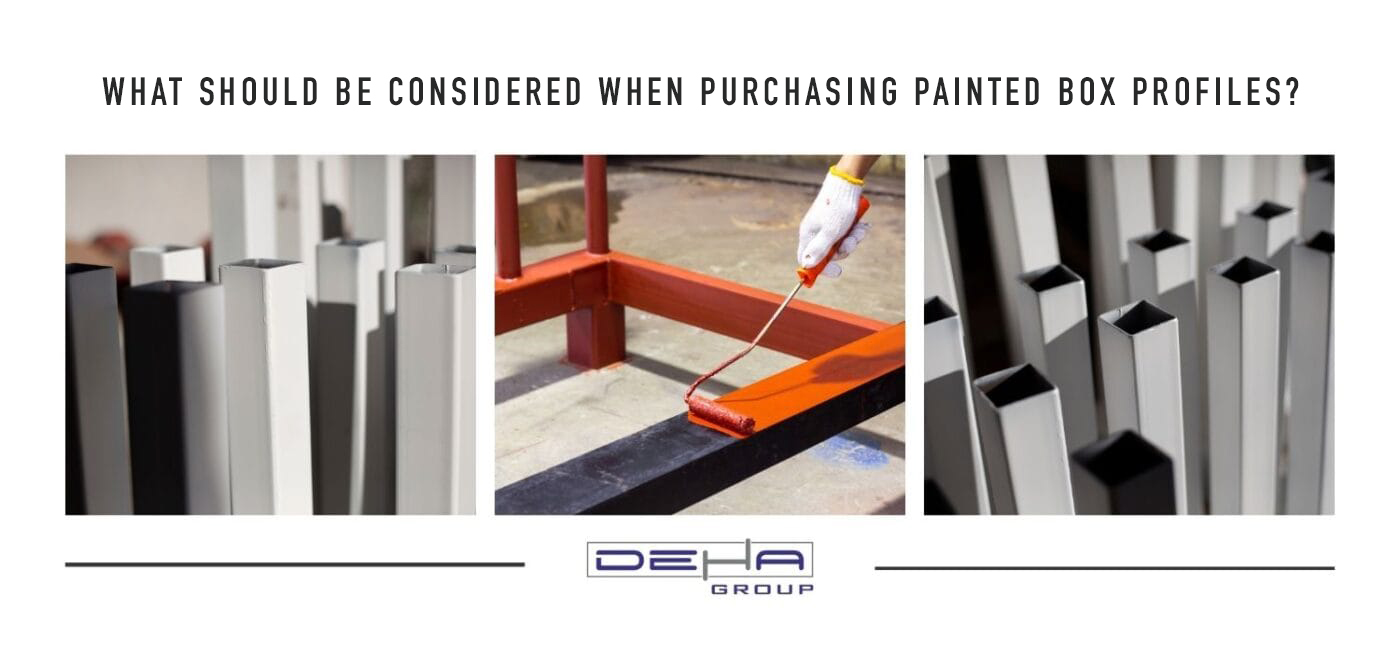
Painted box profile is a type of profile product manufactured by processing metal into a specific shape and applying an aesthetic, protective paint coating. These profiles are typically rectangular or square tubular sections and are used in various industrial and construction applications. Painted box profiles are preferred for both structural and decorative purposes due to their strength and variety of color and coating options. In the construction sector, they are used as framing structures, shelving systems, fences, and decorative elements.
Painted box profiles offer several advantages. Firstly, the surface coating provides protection against corrosion, extending the profile's lifespan and reducing maintenance needs. Additionally, the variety of coating materials and color options provide a wide aesthetic range, allowing them to be used for various decorative purposes with different color and texture selections.
Functionally, the durability and reliability of these profiles are paramount. Their high load-bearing capacities and protective coatings make them safe for use in various applications. Furthermore, their ability to be customized with different sizes and section alternatives offers solutions tailored to the specific requirements of projects. This combination provides an ideal product that meets both aesthetic and functional needs.
The production process of painted box profiles begins with the selection of quality and suitable materials. Typically, steel or aluminum alloys with high strength are used. The choice of material directly affects the durability and performance of the profile. The material is prepared appropriately for the production process and undergoes necessary chemical and physical tests.
During the preparation stage, the material is first cut and shaped into specific dimensions. Box profiles are usually tube-shaped, created by cutting and shaping long metal strips. At this stage, precise cutting and shaping processes are performed to ensure the profiles are of the desired cross-section and length. Additionally, the cleanliness and surface preparation of the material ensure it is ready for the coating process.
Once the material is prepared, the shaping process begins. Metal strips are bent into a certain form to create the box profile shape. This process is typically carried out using a series of machines and equipment. During the shaping stage, it is ensured that the profile is shaped uniformly and evenly to avoid incompatibility during assembly.
After the shaping process is completed, welding operations are performed to join the profile. The welding process ensures that the profiles are joined in a strong and durable manner. During welding, the ends of the profiles are joined, achieving strong structural integrity. At this stage, the quality and strength of the welding are important as they affect the overall durability of the product.
After the shaping and welding processes are complete, the profile moves to the paint coating stage. Paint coating enhances the aesthetic appearance of the profiles and provides protection against corrosion. Using electrostatic powder coating or liquid paint coating methods, the surface of the profile is coated uniformly. During the coating process, it is ensured that the paint is applied smoothly and evenly.
Following the paint coating process, the profiles undergo final inspections. These inspections include checking the coating quality, profile dimensions, and overall appearance. Additionally, various tests are conducted to determine whether the products meet quality standards. After the final inspections, the profiles are packaged and made ready for shipment.
Quality and Standards
The quality of painted box profiles is of great importance both in terms of durability and aesthetics. The most critical factor determining the quality of the profile is whether the standards of the material and paint coating used are met. The material used in the product's manufacturing ensures that the profile is long-lasting and durable. Quality materials reduce the risk of issues such as deformation and corrosion over time. Additionally, the paint coating increases the product's protection against external effects and preserves its aesthetic appearance. Quality control tests guarantee that the product meets certain standards and will be long-lasting.
Another factor affecting quality is the surface coating of the profile. Having a smooth and homogeneous surface coating on painted box profiles is crucial for long-term use. Poor quality coatings can lead to problems such as cracking, peeling, or color fading over time. The quality of the profiling coating method and material directly affects the product's performance. Quality coatings enhance the product's durability and reduce maintenance requirements.
Finally, the certificates provided by the manufacturing companies should also be evaluated in terms of quality. Certificates indicate that the product is produced according to specific standards and that its quality is approved. These certificates increase reliability during the purchasing process and ensure that the product will perform as expected. Certified products offer a more reliable choice in terms of quality.
Types of Paint Coatings and Application Methods
The coating types of painted box profiles determine the product's aesthetic and durability features. One of the most common coating types is electrostatic powder coatings. This type of coating provides high durability and aesthetic appearance. Electrostatic powder paint helps the profile protect against corrosion and offers a long-lasting solution. It also provides a wide range of aesthetic options with various color choices. This coating type is particularly suitable for outdoor uses as it is resistant to UV rays and weather conditions.
Another type of coating is liquid paint coatings. Liquid paint coatings are generally considered a more economical option, but their durability may be lower compared to electrostatic powder coatings. The application process of liquid paint coatings is easier, but in the long term, color fading and surface deterioration issues may occur. Therefore, attention should be paid to the conditions under which liquid paint coatings are used.
Besides the types of coatings, application methods are also of great importance. Proper application of paint coatings maintains the profile's performance and aesthetics. The key points to consider during application include surface preparation, paint application technique, and drying time. A quality coating process ensures the product is long-lasting and aesthetically pleasing. Additionally, choosing expert personnel in the coating process enhances the product's performance.
The correct dimensions of painted box profiles are a critical factor for suitability with their intended use. Incorrect dimensions can cause incompatibility during installation and lead to additional expenses. Therefore, required dimensions should be determined in advance, and it should be ensured that the supplied products meet these dimensions. Correct dimensions facilitate the installation process and enhance the product's performance.
The area where the profile will be used is another factor that needs attention. Different application areas may require different features and durability. For example, profiles with high corrosion resistance should be preferred for outdoor use. These profiles are resistant to weather conditions, UV rays, and chemical effects. For indoor use, aesthetics and color options may be prioritized. Choosing products suitable for the application area increases performance and aesthetics.
The installation and maintenance process should also be considered. Paying attention to specific points during the installation of the profile ensures long-lasting and trouble-free use. Additionally, following maintenance and cleaning instructions preserves the product's performance and appearance. Being informed about the installation and maintenance process extends the product's life and increases user satisfaction.